
Stay curious!
At Chalmers University of Technology, creativity and technology go hand in hand. Here you will experience a vibrant student life – where curiosity leads your way, and sustainability is a beacon.
Explore new ideas in a creative learning environment, together with students from around the world.
Build a career you love and make a difference by tackling real-life challenges together with global industry leaders.
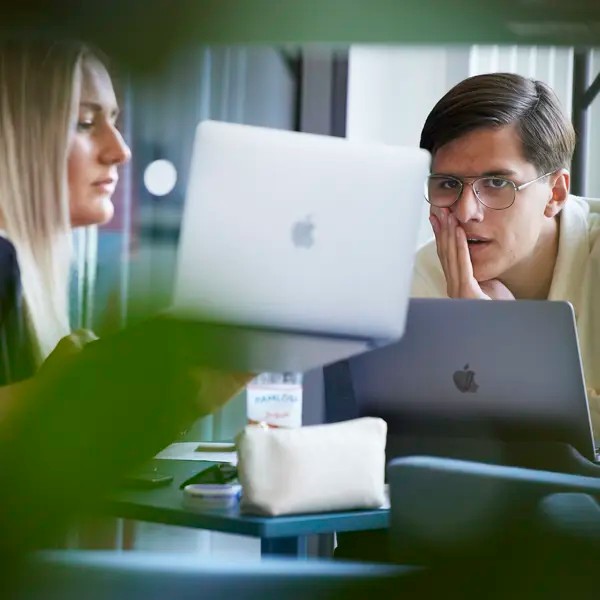
How to apply
Applying to Chalmers is easy, but there are a few things to consider depending on your choice of education. Application periods also differ. Welcome with your application.
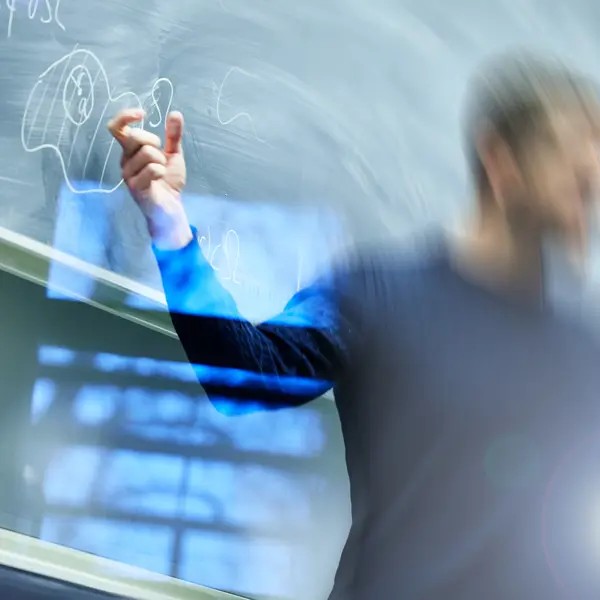
Find master's programme
Qualify for a global career with a master’s degree from Chalmers University of Technology.
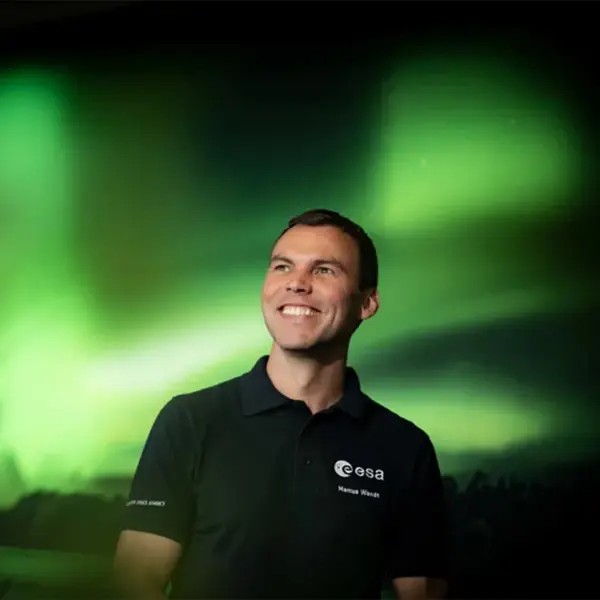
Get to know some of our alumni
Here, some of our alumni, i.e. former students, talk about student life and what they have brought with them
Discover Chalmers' campuses
Take a look inside Chalmers' and discover our world leading facilities.
Get to know us
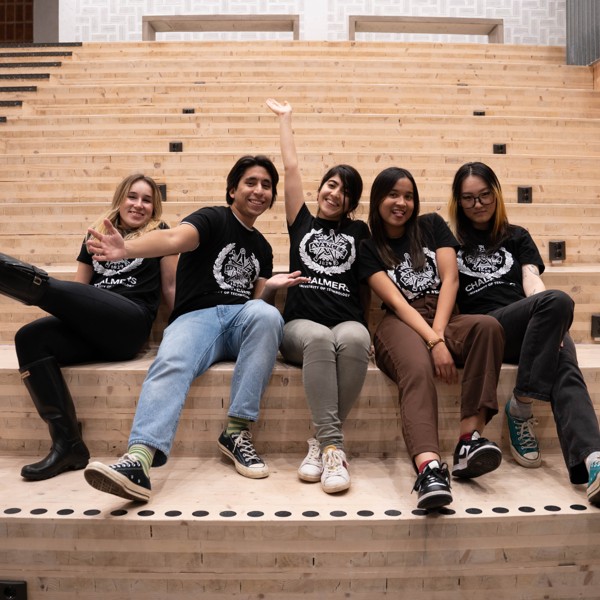
Student blogs
Take part in the stories of our student ambassadors' lives and learn more about what it's like to be a student at Chalmers!
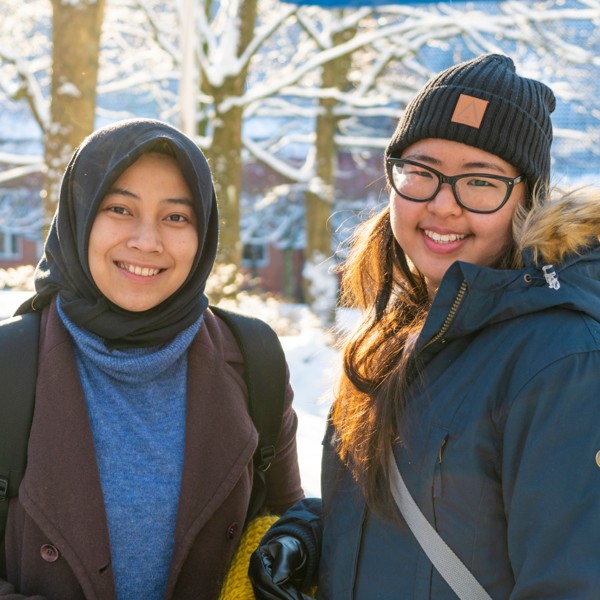
Chalmers master's on Instagram
Our master's students are currently updating about everything realted to student life. Follow us for interesting and fun content!