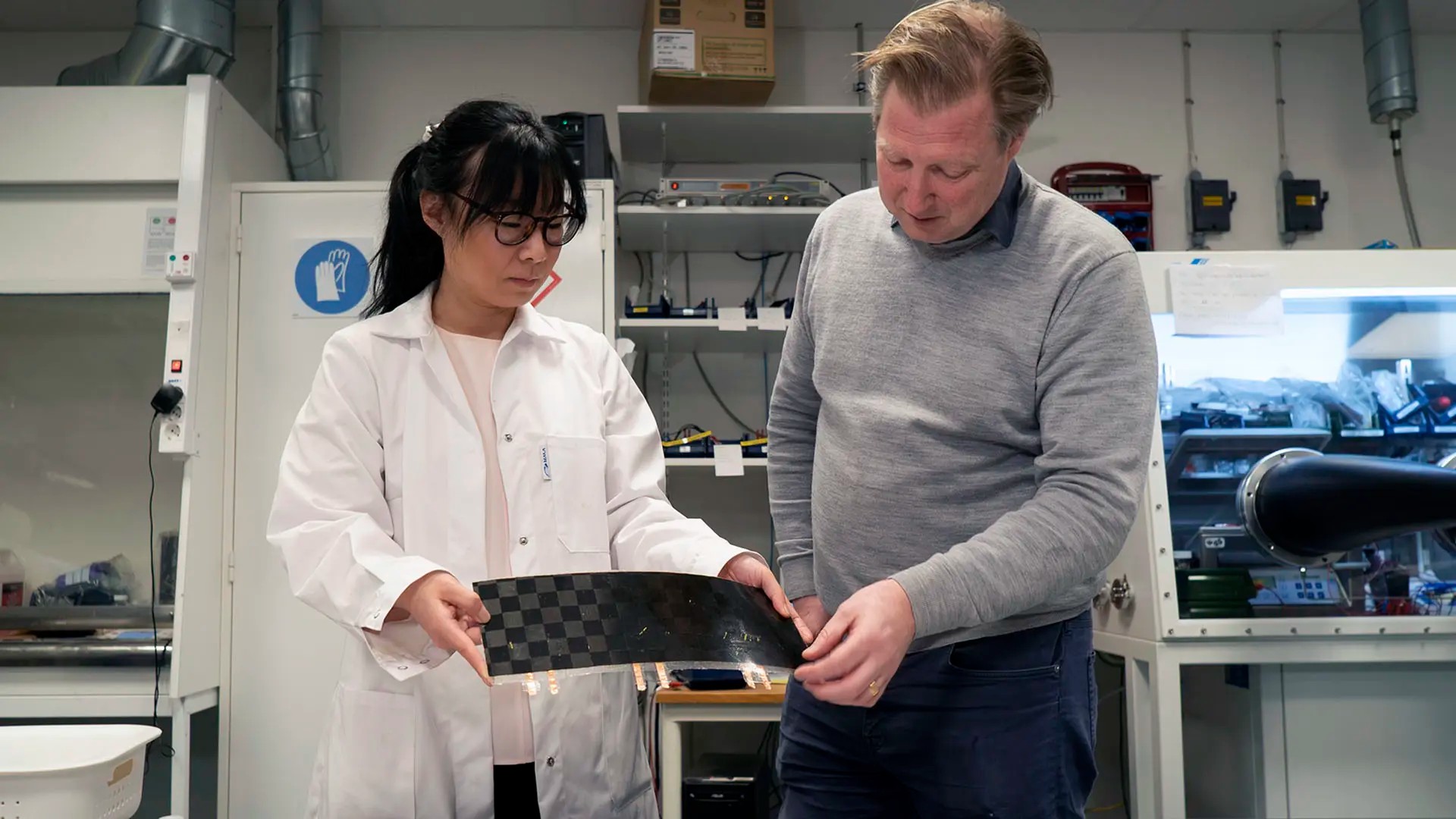
Lightweight structural materials are in ever greater demand. Road vehicles, aircraft, and sea vessels need to reduce greenhouse gas emissions and increase energy efficiency.
To realise these improvements, weight reduction is key. Consequently, increasing the usage of lightweight metals and fibre-reinforced polymer composites in highly optimised structural designs by industry is of the highest priority.
Sports technology is another area where weight reduction is of central importance in maintaining or even improving performance. Sailing, cycling, and ice hockey are just a few examples of sports in which new lightweight technology provides advantages over opponents in terms of easier handling and/or lower resistance.
To facilitate the increase in lightweight design in industry and society, we perform research in material and computational mechanics, especially addressing challenges related to the prediction of material failure and energy absorption under deformation. The current focus is on structural polymer composites in crash applications, for which accurate and efficient material models and numerical methods need to be developed. We have also established a collaboration with Chalmers Sports and Technology to develop lighter and innovative sports equipment. We have built a unique research environment that combines materials science and experimental characterisation with computational material and structural modeling.
Our research is based on excellence in material and structural mechanics combined with a deep understanding of the behaviour of the material under loading and the manufacturing processes of composites. More specifically, we are working on developing high-performance composite materials from thin, discontinuous tapes. We also develop methods for predicting damage initiation in textile reinforced composites; progressive failure modelling in metals and composites, multiscale modelling and homogenisation; damage modelling (CDM and XFEM); and characterisation and modelling of multifunctionality of composites and their constituents.