
Cement, included as a binder in concrete, is the world's most used building material but also accounts for up to 8 percent of global carbon dioxide emissions – with 75 percent of the infrastructure needed in 2050 not even been built yet. At Chalmers, research is ongoing in several different research projects to reduce the proportion of cement – but also to let the cement work for us.
Arezou Baba Ahmadi is an Assistant Professor at Building Technology, Department of Architecture and Civil Engineering, and researches new cement-based materials with a lower environmental impact than the current ones. She and her colleagues in the research group she leads work on a broad front with different types of techniques for new cement. The starting point is that there is no general solution, but that different methods need to be combined.
One solution is to add so-called pozzolanic materials, used by the Romans in the form of volcanic ash in their concrete 2,000 years ago, to reduce the proportion of cement. A recently started project funded by the Thomas Family Foundation is about assessing the capacity of such concrete to capture carbon dioxide from the air, a variant of the popular CCS technology. In this way, the need for cement can be reduced while at the same time storing the captured carbon dioxide in the material – for a more efficient reduction of the amount of carbon dioxide emitted in the cement manufacturing process.
One solution is to add so-called pozzolanic materials, used by the Romans in the form of volcanic ash in their concrete 2,000 years ago, to reduce the proportion of cement. A recently started project funded by the Thomas Family Foundation is about assessing the capacity of such concrete to capture carbon dioxide from the air, a variant of the popular CCS technology. In this way, the need for cement can be reduced while at the same time storing the captured carbon dioxide in the material – for a more efficient reduction of the amount of carbon dioxide emitted in the cement manufacturing process.
– In the research group, we have focused on different types of solutions that are about becoming less dependent on the most common type of cement known as Portland cement. The technology of carbon dioxide capture is an important piece of the puzzle, but if we want to achieve carbon dioxide neutrality with lower costs for the manufactured material, we need to supplement with more alternatives, says Arezou.
Slag from green metal industry put to use
In a new major project financed by The Swedish Agency for Economic and Regional Growth, Chalmers together with the manufacturer Cemvision as well as LKAB, Vattenfall and RTW Aachen, will further develop and combine two established cement technologies to produce a cement with a world-unique ultra-low carbon footprint. Some of the current binders, like SSC (Super Sulfated Cement) are still relatively unknown in the Swedish construction industry, and manufacturer Cemvision will develop a contemporary version of yet another binder with the advantage that it can be produced using residual material from primarily the metal industry, with the carbon dioxide being removed already in the initial process.
– The steel and metal industry generates approximately 1.3 million tons of slag per year in Sweden alone, and at the moment only a third of the slag can be used as a cement substitute. With our project, we are developing technology to be able to use up to 90% of these residual materials as cement, says Arezou.
The old carbon dioxide-intensive blast furnace-based technology traditionally used by the steel industry is gradually being phased out in favor of direct-reduced iron technology that also has potential for electrification. The supply of blast furnace slag will thus decrease and worsen the global shortage of cement replacement materials with low carbon dioxide emissions. The remaining slags, like the future slags from the electric arc furnaces of the electrified steel industry, also require new technology.
– We develop technology to maximize the usability and carbon dioxide benefit of both existing and future residual materials, regardless of the type of cement that will dominate the Swedish market in the future. In this project, we have both manufacturers and end users with us, which gives a strong potential for application, says Arezou.
Development of materials for future needs
The target group for the new material is primarily the concrete industry and socially useful companies that require large quantities of concrete in housing, infrastructure, mining, energy production and other types of construction. Something that has also been an incentive for actors such as LKAB and Vattenfall to be part of the project. When asked if the time for cement is up and what comes next, Arezou seems certain;
– What will change is the way we optimize the material, but a product that is easy to manufacture, cost-effective, works as a binder and is readily available in the local environment where it is produced will always be needed. What we call it and how it is made may change, but the concept will remain, says Arezou Baba Ahmadi.
*CemVisions Belitic Calcium Sulfo Aluminate cement (BCSA)
**SuperSulfat cement (SSC)
About the projects
The project "Post Norm Supersulfated Cement" is a collaboration between RWTH Aachen University, Vattenfall, LKAB och Cemvision. The total budget for the project is 24 MSEK whereof Tillväxtverket, The Swedish Agency for Economic and Regional Growth, supply 20 MSEK.
The project “Evolution of pozzolan incorporated concrete: Resistance to Carbonation (Carbo-Crete)" is financed with 7,5 MSEK by The Thomas Family Foundation.
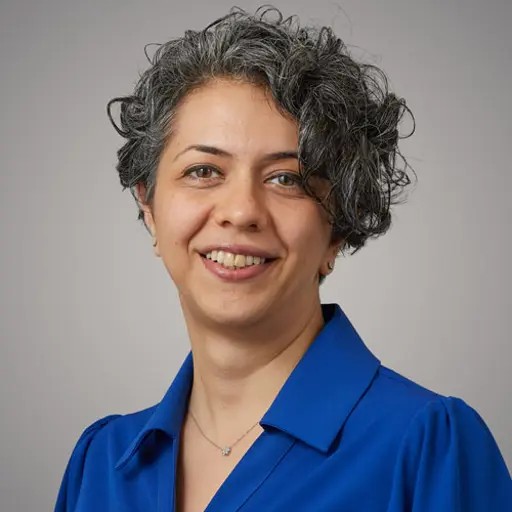
Arezou Baba Ahmadi
- Associate Professor, Building Technology, Architecture and Civil Engineering