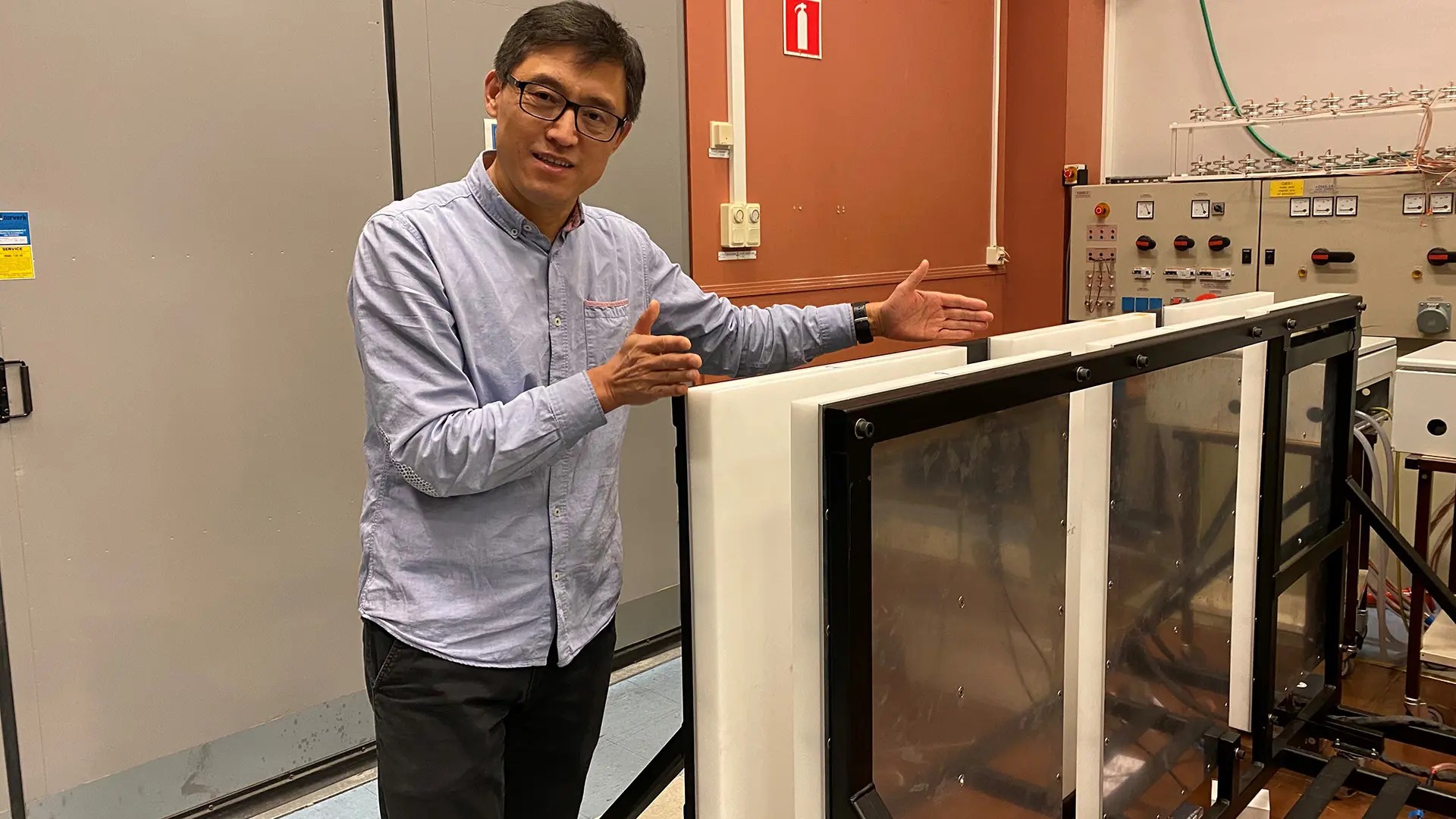
Researchers at Chalmers have developed an induction technology that enables battery charging without the help of a human or robotic arm. The technology is also so complete that it can soon be presented to industry.
A new type of semiconductor based on silicon carbide. And a newly developed copper wire, as thin as a human hair. These are a couple of factors that suddenly made it more realistic to transmit high power through air.
Charging induction is the new thing
Electric toothbrushes have been doing it for decades. In recent years, cell phones and other portable electronics have picked up the technology. But for the high power required to charge the batteries in an electric vehicle, the wireless option has so far appeared to be too complicated and ineffective.
However, charging with the help of induction now seems to be facing a breakthrough even in the case of battery vehicles - above all when charging needs to happen often and where the environment is demanding. For example, for an electric city ferry.
Charge without a human or robotic arm
This would mean that electric ferries in regular traffic across waterways in cities, which can be found in Gothenburg and Stockholm, do not need the help of a person or robotic arm to charge batteries. The same applies to city buses or driverless electric vehicles used in industry, mining, and agriculture.
Yujing Liu, Professor of Electric Power at the Department of Electrical Engineering at Chalmers, is particularly focused on renewable energy conversion and electrification of the transportation system.
“You can have a system built into the wharf that charges the ferry at some stops, at the same time as passengers get on and off. Automatic and completely independent of weather and wind, charging can take place 30 – 40 times per day. This is probably the most obvious application,” says Yujing Liu.
“Even for electric powered trucks of the future there is perhaps a potential application. Then the motive is rather that these will have to be charged with such high power that a charging cable becomes very thick and heavy and thus difficult to handle”.
New possibilities thanks to the development of materials
According to Yujing Liu, it is the rapid development of a handful of components and materials in recent years that has opened for new possibilities.
“A key factor is that we now have access to high power semiconductors based on silicon carbide, so-called SiC components. As power electronic products, these have only been on the market for a few years. They allow us to use higher voltage, higher temperature, and much higher switching frequency, compared to classic, silicon-based components”, he says.
This is important, because it is the frequency of the magnetic field that sets the limit to how much power can be transferred between two coils of a given size.
Four times higher frequencies
“Previous systems for vehicle wireless charging have used frequencies of around 20 kHz, much like a normal stove top. They became bulky and the energy transfer was not very efficient. Now we work with frequencies that are four times higher. Then induction suddenly becomes attractive”, explains Yujing Liu.
He adds that his research group is in close contact with the leading manufacturers of SiC modules in the world, two companies based in the US and Germany respectively.
“With them, rapid product development takes place towards even higher currents, voltages, and effects. Every two or three years, new versions are launched, which can withstand more. These types of components are important "enablers" with a wide range of applications in, for example, electric vehicles, so not only for inductive charging”.
Another recent technological leap concerns the copper wires in the coils that send out and receive respectively the oscillating magnetic field that forms the actual bridge for the energy flow across the air gap. Here, the goal is to use as high a frequency as possible.
“Then it does not work with coils looped with ordinary copper wire, it would lead to very large losses at high frequency”, says Yujing Liu.
Instead, the coils are now made up of braided 'copper ropes', consisting of up to 10,000 copper fibres, each only between 70 and 100 micrometres thick. Much like a strand of hair.
Such braids, of so-called litz wire, adapted for high current and frequencies, have also only been commercially available in the very last few years.
A third example that Yujing Liu highlights is a new type of capacitors that are used to add the reactive power that is a prerequisite for the coil to be able to build up a sufficiently powerful magnetic field.
Yujing Liu emphasises that charging electric vehicles contains several conversion steps – between direct current and alternating current and between different voltage levels.
“So, when we say that we have achieved an efficiency of 98 percent from direct current in the charging station to the battery, that figure may not mean much if you do not carefully define what is measured”, he reasons.
“But you can also put it this way: Losses occur whether you use ordinary, conductive charging or charge with the help of induction. The efficiency we have now achieved means that the losses in inductive charging can be almost as low as with a conductive charging system. The difference is so small that in practice it is negligible, it is about one or two percent”.
Numbers attract attention
He adds that the results published by his research group have attracted a lot of attention.
“We are probably among the best in the world in terms of efficiency in this power class, between 150 and 500 kW”.
Yujing does not think that induction charging will eventually replace charging with a cable.
“I drive an electric car myself and do not see that I would have any use for induction charging in the future. I drive home, plug in... it's no problem”.
Is wireless charging a more sustainable technology than charging in the usual way?
- One should probably not claim that the technology itself is more sustainable. But it can make it easier to electrify large vehicles and thus speed up the phasing out of, for example, diesel-powered ferries.
Text: Sandra Tavakoli
For more information, contact:
Yujing Liu, Professor of Electrical Power Engineering at the Department of Electrical Engineering, Chalmers
yujing.liu@chalmers.se
+46317721660
Facts about induction charging
- Charging using induction means that current can be transferred over a short distance, for example through air, water, and other non-metallic materials, without any contact or conductor.
- The principle is the same as that used in the induction cookers found in many kitchens. A high frequency alternating current through a coil produces an oscillating magnetic field.
- But unlike cooking, where heat development is the point, inductive charging means that a second coil, on board the vehicle, captures the energy in the magnetic field and converts it into alternating current again - which, after rectification, can recharge the batteries.
- The heat generated in the process means that part of the energy to be transferred is lost. Minimising heating as far as possible is therefore an important goal for technology development.