
Additive manufacturing – or metal 3D printing – is a revolutionary technology with the potential to change the entire manufacturing landscape. With additive manufacturing it is possible to create innovative and advanced metallic components in a completely new way, with brand new performance and functionality.
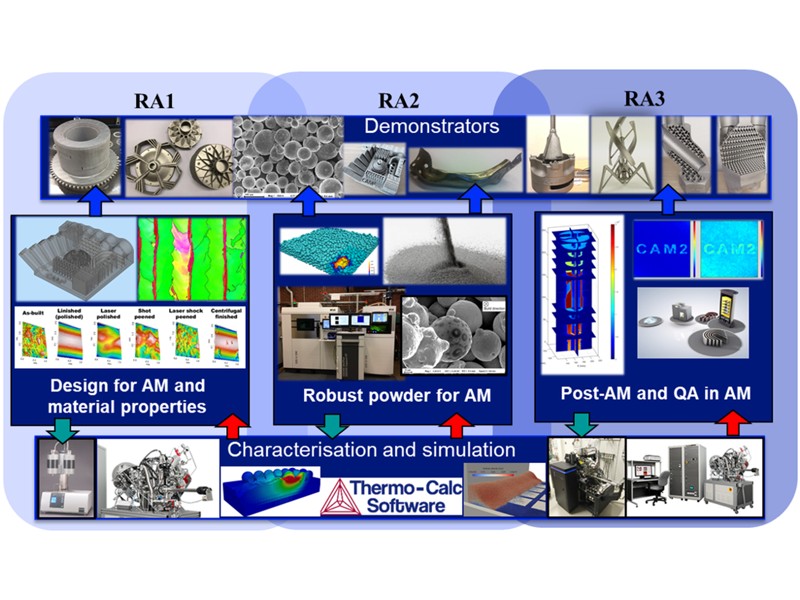
When it comes to metal additive manufacturing, powder-based metal additive manufacturing technologies constitute the core. The mission of CAM2 is to further revolutionize the additive manufacturing technology by bringing the advantages from powder technology – an area of materials development where Sweden is particularly strong and is a world-leader in metal powder production. This naturally determines the main focus of CAM2 - powder material development for powder-based metal additive manufacturing.
We act in three research areas
The overall goal of the centre is the further development of the competences across the entire metal AM process chain.
CAM2 consists of three Research Areas:
- Design for Additive Manufacturing and materials properties (RA1)
- Robust Powder for Additive Manufacturing (RA2)
- Post-AM treatment and quality assurance in AM (RA3)
The project portfolio includes 21 projects of different types, PhD student project, industrial PhD student project and post-doc projects.
Design for additive manufacturing and material properties (RA1)
We focus on in-depth understanding of the microstructure and defect formation during powder bed fusion processing of metallic materials and its impact on material properties, including both static and dynamic material properties. Productivity increase and its impact on material properties is also studied to improve build rate and improve cost effectiveness of metal AM. These activities is supported by advanced materials characterization, including large-scale facilities, to assure necessary support for material and process development in other research areas as well.
Objectives
- to establish design limitations of powder-based AM in dependence on material and technology (PBF-LB, PBF-EB, BJ, DED)
- to establish correlation between AM material properties in dependence on AM technology - PBF-LB, PBF-EB, BJ and DED
- to establish correlation between AM material properties and AM process parameters for PBF-LB and PBF-EB - Microstructure, static and dynamic mechanical properties
- to establish impact of different surface features and internal defects on the fatigue life of AM components
- to establish the limits of productivity in powder-bed AM allowing to achieve robust processing of structural components with density above 98 percent.
Contact
Robust Powder for Additive Manufacturing (RA2)
Objectives
- AM-relevant properties of the powder feedstock
- Sustainability of metal AM
- Powder standardization – ASTM, ISO, SIS, etc.
- Reusability of the powder
- Novel AM materials – Fe, Al- and Ni-base, HEA, materials for electrification, etc.
Contact
- Full Professor, Materials and Manufacture, Industrial and Materials Science
Post-AM treatment and quality assurance (RA3)
Objectives:
- Surface integrity optimization
- Novel post-AM technologies
- In-situ process monitoring
- Machine learning for quality assurance
- NDT in AM
Contact
- Head of Division, Materials and Manufacture, Industrial and Materials Science