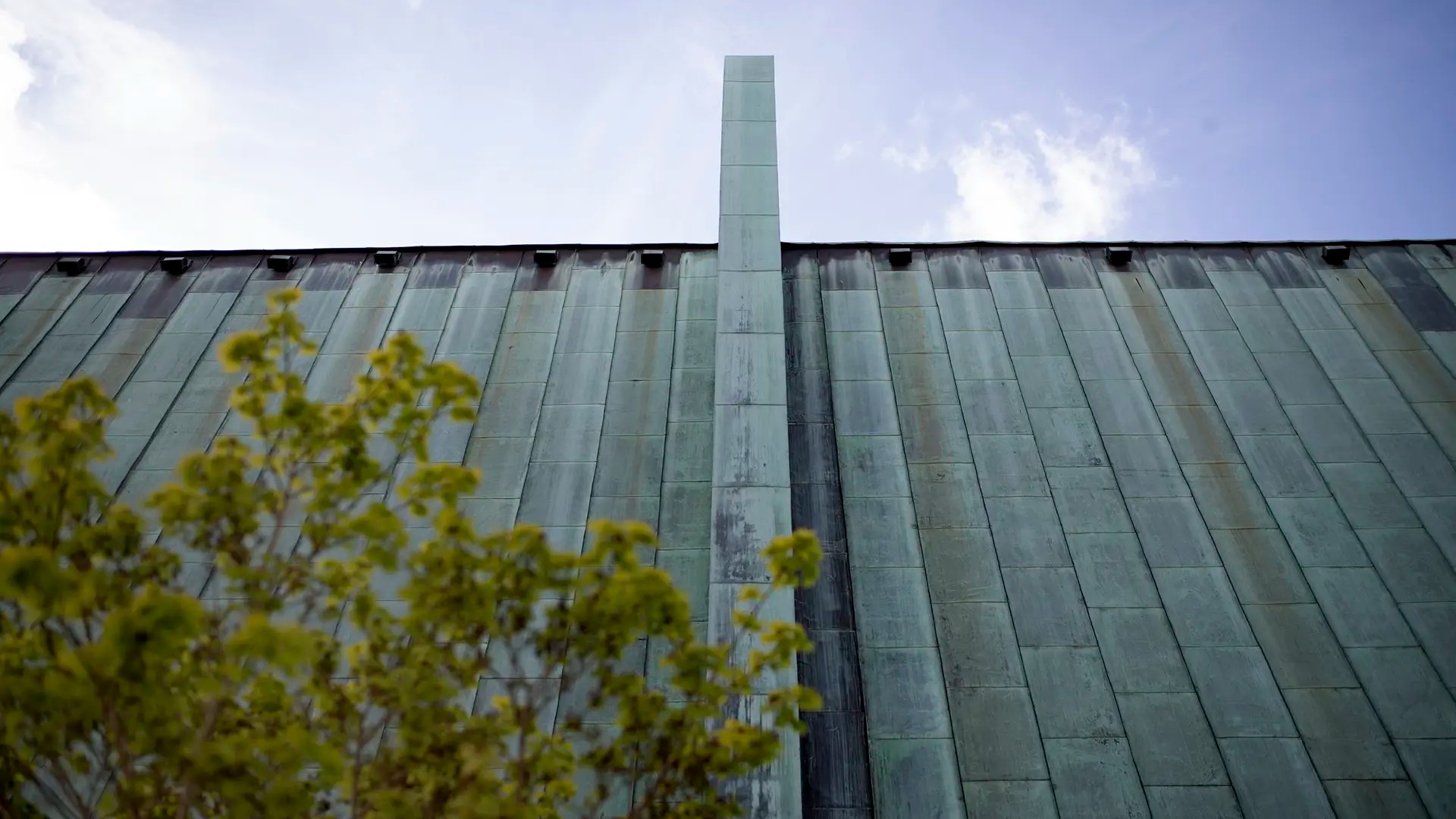
A genuine business interest and a desire to develop a more efficient and sustainable energy system encourages Göteborg Energi to be an active partner in the co-operative activities of the CPP.
“We obtain access to new knowledge that we can use in our existing facilities and in those that we will build and buy in the future. This knowledge cannot be purchased off the shelf. In addition, we get a very good and knowledgeable collaborator that we can consult when making different decisions”, says Bengt Göran Dalman, who is Business Area Director at Göteborg Energi.
E.ON, the SP Swedish Technical Research Institute, Valmet, Akademiska Hus, and Göteborg Energi: the list of external partners is long. Read here what they think about this co-operation.
Göteborg Energi contributes to the development of the technology and sells more heat
Already when Bengt Göran Dalman was studying at Chalmers and attended lectures given by Professor Bo Leckner, he became convinced that district heating, and the power plant technology in particular, represented highly energy efficient smart solutions for the heating of cities and towns. Bengt Göran Dalman emphasizes that as a municipally owned commercial enterprise, Göteborg Energi has a social responsibility to contribute to research towards a better environment.
“My motivation”, he says, “is to be part of developing a more efficient energy system that we can pass on to our children and grandchildren, an energy system that consumes fewer resources and that is good for both the environment and the climate”.
Designing the connection of the district heating lines to the Chalmers Power Central
When the first collaboration between the CPC and Göteborg Energi was inaugurated, Bengt-Göran Dalman was working as a planning engineer at Göteborg Energi. He designed the district heating interlink to the CPC, so that the excess heat produced at the CPC could be transferred to the district heating system and conversely, that in periods of shortage, heat could be provided to the CPC. During the second phase of the co-operative project, when the circulating fluidized bed boiler was built, he was involved in drawing up the contract and was the project manager for the construction of the boiler. He was also active in making the decision to fund the reconfiguration of the boiler to a biogasifier in 2008.
Contribute to the development of the technology and sell more heat
Göteborg Energi took on the project management role and bought up the service to rebuild the boiler, as per Henrik Thunman’s instructions, from the boiler manufacturer Valmet. Moreover, Göteborg Energi financed the gasifier, which cost SEK 13,500,000. The results obtained from the tests conducted in the gasifier were subsequently used by Göteborg Energi to guide the construction of a much larger research facility on a more commercial scale, as part of the GoBiGas project.
Göteborg Energi has also established a cooling facility at the CPC, which exploits cooling from the excess heat from the district heating system to cool the buildings at Chalmers.
“We want to contribute to the development of the various technologies for this type of combustion. At the same time, this is a commercial deal in which we can sell more heat than we would have previously, and we can purchase heat for the district heating network. In addition, the district heating business has become more successful and a more established product within the Swedish energy system thanks to the co-operation with the CPC, and for that we are grateful”, says Bengt Göran Dalman.
For E.ON, co-operation with the CPC results in lower emissions
The energy company E.ON and Chalmers conduct a joint project on the combustion and gasification of biomass. Currently, the new technology is being tested in one of E.ON’s boilers in Norrköping.
“If everything works as it should, we will have adopted an idea from the research area and demonstrated that it works in large boilers. The next step will be to investigate whether it can be commercialized by subjecting it to continuous operation. Very few research projects progress this far”, says Bengt-Ake Andersson, who is responsible at E.ON Värmekraft Sverige for liaising with universities and colleges.
In 1982, Bengt-Åke Andersson was studying energy technology at Chalmers and was carrying out experimental work in the boilers at the CPP. After completing his doctoral studies, he began working with the boiler manufacturer Valmet (formerly Kvaerner/Metso). In 2007, it was time for an assignment at E.ON, which both orders and uses boilers.
In 2008, the CEO of Swedish E.ON decided to launch a 10-year collaboration with Chalmers. In part, the co-operation is concerned with training in nuclear power technologies to cope with the change of generation, but it also deals with the wider topic of energy research, an area in which Bengt-Åke Andersson has fostered research at the CPP.
Time is as important as money
A joint project on combustion technology is currently underway. For a period of 3 weeks, a new bed material was tested in the Chalmers boiler. The tests went well. The next step was for the Chalmers researchers to conduct the same tests in a larger plant in E.ON’s boiler 14 at Händelöverket, Norrköping. The experiment was successful.
“This partnership sits well with E.ON’s strategy of ‘cleaner and better’. That is exactly what this is. Our hope is that here will be fewer emissions and a more efficient process”, says Bengt-Åke Andersson.
E.ON also wants to know if there are any other characteristics of the bed material that remain to be discovered. According to Bengt-Åke Andersson: “It is only when testing on a real-life scale that one can see everything”.
“A key factor in the success of the collaboration between E.ON and Chalmers is the effective decision structure”, Bengt-Åke Andersson points out, “It is a small organization with clear goals. The collaboration with Chalmers is an unusually successful project”.
Bengt-Åke Andersson believes that continuity is an underrated component in many R&D collaborations.
“In my experience, it takes 10 years to reach the frontier of research. This is how long it took for Chalmers in this case. Time is just as important as money. For companies to be able to assimilate the results of university research, both patience and commitment are essential”.
Valmet builds boilers in exchange for valuable knowledge
Valmet Power has built both boilers and the gasifier at the CPC. In return, they have gained valuable knowledge, which has been used to develop more efficient boilers that to meet all the environmental requirements.
“The partnership has helped us to finetune our technology so that we can offer our clients strong guarantees, with regard to emissions among other issues”, says Margareta Lundberg, who is responsible for product development and product support at Valmet in Gothenburg.
Margareta Lundberg points out that Valmet Power has benefited from the collaboration with Chalmers in several different ways. Besides the emissions issue, they have received help with understanding how the boiler should be designed to attain optimal performance. The partnership has also led to a continuous transfer of knowledge, whereby engineers and scientists have started working at Valmet.
Throughout her career, Margareta has engaged in research and development at the company. The main area of interest has been fluidized beds with a focus on environmental issues. Today, Valmet Power works primarily with recovery boilers for the pulp industry and biofuels, but also with the wastes from fluidized beds of the same type as found at the CPC.
Testing on a small but industrial scale
When Generator (as the company was called then) built the first Bubbling Fluidized Bed boiler at Chalmers in 1981, the collaboration was part of product development. When the bubbling bed proved to to have various drawbacks Chalmers wanted to research circulating fluidized bed technology as a more promising alternative. Generator also wanted to know more, and so it built a new boiler in the CPC in the late 1980s.
During the period 1989–1991, Valmet Power and the Insitute for Energy Technology collaborated on a joint project to find out more about the emissions in the flue gases that exit the chimney.
“It was a very good project because we were able to test on a small, yet industrial scale at Chalmers. It is not so expensive to purchase fuel for a smaller facility and besides most of the cost was paid by Chalmers for heating, and there is no fear that one can mess up so badly that a whole town becomes cold. When we conducted experiments at the CPC, we found that we could run really large boilers and profit from the lessons learnt along the way”, says Margareta Lundberg.
Scientists can dig deep
Thanks to the sophisticated measuring equipment attached to the Chalmers boiler, one could measure numerous factors that could not be measured elsewhere, to obtain a fundamental understanding of the process.
“The combination is unique, in that the boiler is of sufficiently large scale that the results are easy to apply in the industrial setting, while at the same time the scale is sufficiently small that researchers can conduct in-depth investigations to really understand what is happening rather than just to observe what happens”, says Margareta Lundberg.
Dared to make decisions and invest money
In recent years, the co-operation has focused on gasification, which is a completely new process. Claes Breitholtz, who is employed at Valmet Power, also having his PhD at Chalmers, worked part-time for 5 years on the gasification project with Henrik Thurman and his colleagues. He participated in the experiments and took on board the issues relevant to the industry, while Henry Thurman contributed the academic aspects. This combined body of knowledge was valuable in directing Göteborg Energi's commitment to the gasification of biomass in the GoBiGas project, in which Claes Breitholtz is engaged currently.
“As a company, we have been able to contribute with industrial relevance and to help researchers do things what will be of benefit, both to us as manufacturers and to our customers”, says Margareta Lundberg.
She is convinced that the network that was formed initially between the four partners, Valmet Power, Chalmers, Göteborg Energi, and Akademiska Hus, has been crucial to the success of the CPC. “These were four parties who dared to take crucial decisions and to invest money”.
SP wants to be close to both industry and academia
The SP Technical Research Institute of Sweden has co-operated with Chalmers and scientists at the CPC in several different projects ove a long period of time.
“At SP, we want to be close to industry and applications, but we also want to be close to academia and basic research. The collaboration at the CPC is a very good bridge between the academic environment and industrial application. There are few such environments”, says Andreas Johansson, Head of Unit at the SP Technical Research Institute of Sweden.
He points out that the CPC is a real plant of commercial size, unlike a laboratory reactor where everything happens under very controlled conditions, with many simplifications.
“If the researchers can show that something works at the CPC, it is easier to transfer the knowledge to industry”, says Andreas Johansson.
Using waste to reduce greenhouse gases
Andrew describes himself as a ‘waste nerd’.
“Using the waste that is currently being burned in the power-heat sector is one of the lowest-hanging fruit to bring more renewable fuel into the system and reduce the levels of greenhouse gases in the atmosphere”.
He believes that the majority of European countries are extremely bad at following the examples set by Sweden, Germany, and Holland in establishing energy recovery from waste that can be incinerated.
“My big motivation is to increase and improve the use of more difficult fuels in an environmentally sound manner”.
Close to the industry and applications
Very many of those who are involved from the SP side have been active earlier in the environment at CPC, either as graduate students or trainees. This has helped to retain trained researchers in the scientific community. In the case of Andreas Johansson, he began to co-operate with the CPC when he was a graduate student and was examining the incorporation of biofuels into coal-fired boilers. Since then, he has been involved at SP in various studies aimed at the development of measurement techniques, combustion of difficult fuels, gasification, and the distribution of fuel in the gasification reactor, as well as in a project that investigates the possibility of achieving so-called two-step combustion.
Good at adapting the CPC to new requirements
“One reason that the infrastructure around the CPC has worked so well is that Chalmers has been good at adapting the facility to new demands”, says Andreas Johansson. “The trend towards gasification is an example of how one has met the challenges from the outside world”.
While SP has access to well-functioning and continuous test environments and test beds at the CPC that provide relevant results, Chalmers benefits from being exposed to new hypotheses and ideas and acquires the means to do experiments.
Research at both the system level and experimental level is needed
Andreas Johansson has noted that students nowadays are more interested in research at the system level, rather than experimental research.
“While a model can always be good, it is only when one applies the model that one discovers what is not consistent with the theory. Whereas the global need for experimental research has not diminished, the fear that this research will entail extra costs seems to have increased. To achieve success, we need research at both the system level and the experimental level."
The CPC plays a crucial role in major investment in biogas
The Göteborg Energi biogas plant, GoBiGas in Ryahamnen, is the first in the world to use gasification technology on a large scale.
“Co-operation with Chalmers and the CPC has played a crucial role in the venture”, says Åsa Burman, who is the Project Manager and CEO of GoBiGas at Göteborg Energi.
On March 12th, 2014, Göteborg Energi inaugurated a new demonstration plant for the production of biogas. The goals are a sustainable society and a fossil-free future, a vision that Göteborg Energi shares with Chalmers.
Already in 2005, at a time when Göteborg Energi was starting to look at gasification, discussions with Chalmers led to Göteborg Energi investing in a gasifier at the CPC, to test and develop the technology. Valmet Power built the gasifier, which is the largest in the world for research purposes.
The CPP is a prerequisite for investment
Since then, Göteborg Energi and Chalmers have carried out numerous experiments in the CPC gasifier and tested different fuels. The knowledge gained has been used to design and deploy the GoBiGas plant, which uses the same technique, indirect gasification of forest waste.
“If we had not started with building the smaller gasifier at the CPC, then we would not have gone ahead with GoBiGas project. The Chalmers plant is sufficiently large that the derived results can be relevant. As we are now doing the same thing on a larger scale, we can see that what we tested in the Chalmers gasifier actually works. The CPC is a unique and large facility for testing, as is this gasifier”.
A positive example of the Gothenburg spirit
Chalmers has also trained many who work on the project.
“As we build a brand new technology, we need to nurture our own technical expertise. It has been critical that we have been able to build this facility”, says Åsa Burman, who perfomed her thesis work at the Division of Energy Technology at Chalmers.
“Behind the success of GoBiGas project is a great willingness to work together to achieve results”, says Åsa Burman.
“The Gothenburg spirit is sometimes seen as something negative, but this is a positive example, where academia, Göteborg Energi, as a municipal corporation and business work together to achieve something important. We need to replace fossil fuels, and this is a very good way to do that”.
Akademiska Hus takes care of the operational activities so that scientists can conduct research
Akademiska Hus is responsible for the operation of the CPC. The staff caters to researchers' requests while at the same time providing the buildings at Chalmers with heating and cooling.
“We have a professional management organization, which enables researchers to devote themselves to research rather than to managing the operation of the boiler”, says Per Löveryd, who is the Operations Manager at the CPC.
At the CPC, researchers can conduct research on a real production scale at a cost that would otherwise only be sufficient for research on the laboratory scale. Since the boiler is operated on a commercial basis by Akademiska Hus and produces heat for Chalmers, only the marginal cost of the research needs to be covered.
“Our service is included in the rent, which of course is very inexpensive, compared to a situation in which the researchers had to pay for every hour that they used the plant”, says Per Löveryd.
Operation of the plant is adapted to the wishes of the researchers
Every Friday, the operational staff meet with the researchers at Chalmers to go over what has happened during the week and the plans for the following week. To allow the researchers more time in the CPC, the first shift starts at 06:00 and the last shift ends at 18:00. The staff members are also prepared for any activities or problems that might occur at night or on the weekend, for example, when the bed material needs to be changed.
From the laboratory to industrial-scale research
Per Löveryd started working here in 1973, when he trained to become am operational engineer. At that time, the CPC functioned as both a production and laboratory facility, although intensive research was not carried out. Per Löveryd retunred to the CPC in 1980 as a machine foreman, at a time when new research projects were being established around the fluidized bed technology, which Bo Leckner developed and which has inspired the research conducted here ever since.
“Thanks to the well-functioning infrastructure and skilled staff, it is not so expensive to rebuild and build a new”.
The first boiler that was built was in use up until 1990. Today, it serves as an auxiliary boiler that is fired with bio-oil.
“There were serious concerns about the boiler and one had to be really enthusiastic. The boiler was large and you had to dump a lot of steam. Flowing stream makes a lot of noise. We drove the pan with a loud bang for 5 years!”
Personnel with extensive knowledge of the plant
In 1989, researchers developed the fluid bed technology, and in 1990, they built a circulating fluidized bed boiler in which sand is transported around in the boiler. The circulating fluidized bed boiler worked fine from the very start. Initially, it was fired with coal. Later, renewable fuels and biomass in the form of chips were delivered in trucks twice a day. The facility is also approved for the burning of waste.
In 2008, the biogasifier was constructed; it has been used for various experiments, the results of which have then been used in Göteborg Energi's large investment in the gasification of biomass, the GoBiGas project.
“A big advantage for Chalmers is that the operating personnel have extensive knowledge of the plant and are good at taking advantage of and maintaining good working conditions. While we continually rebuild in accordance with the researchers’ wishes, nothing is discarded needlessly”, says Per Löveryd.