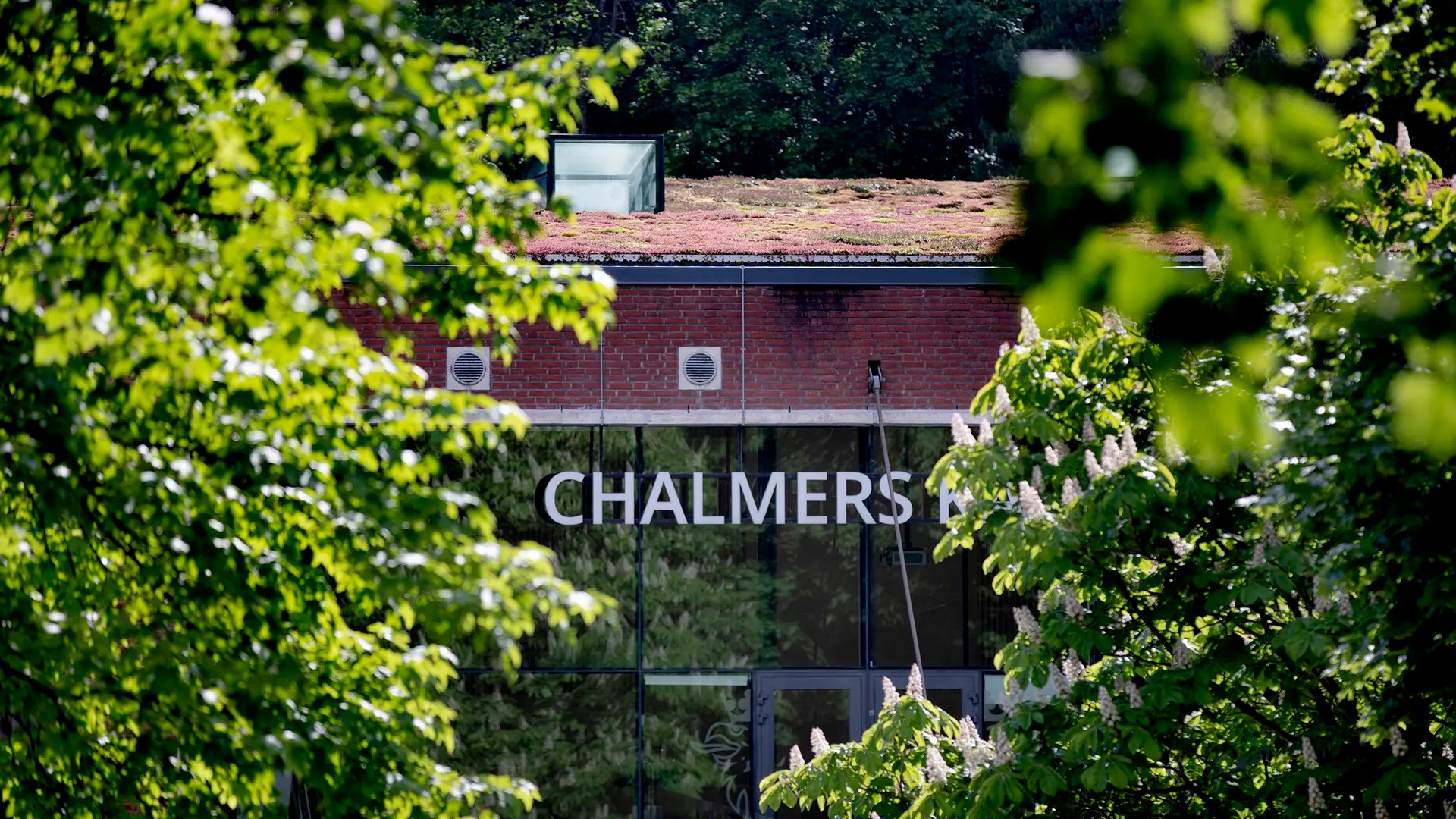
The story of the Chalmers Power Central (CPC) begins in 1947 when the first boilers were built, although it was only after the oil crisis of the 1970s that the research program really took off. Professor Bo Leckner was the driving force behind efforts to find partners who would invest time and money in new boilers.
“One can count publications and scientific citations, but the important thing is if someone reaps the benefit of what we do. Then it's good. Then we have succeeded”, says Bo Leckner.
The first boilers at CPC were built in 1947 to produce heat for the buildings. There were two steam boilers that were fired with coal. The heat was transported through pipes to the various buildings, which was a novel development at the time. The aims were to examine the characteristics of district heating and to demonstrate the advantages of using a centralized heat production unit to heat homes and offices instead of each building having its own boiler.
During the initial decades, there was no external funding for the research conducted at the CPC. Interest in and funding for research in the energy field expanded first in the years after the oil crisis of the early 1970s.
Access to new technologies attracted boiler manufacturers
In 1973, Bo Leckner tutored a student who wrote his thesis on fluidized bed technology, a technique that could be used to exploit difficult-to-fire coal.
“It was not difficult to convince the Chalmers administration and the boiler manufacturer Generator to replace the old boilers with new ones and thereby gain access to the new technologies”, recalls Bo Leckner .
By 1982, the older boilers had been replaced by the first demonstration plant, called a fluidized bed boiler, with the financial support of Nutek, the predecessor of the Swedish Energy Agency. After a while, it became obvious that the technology did not work so well. The steam tubes contained in the bed became corroded and destroyed.
“Had we simply used ordinary laboratory equipment we would never have discovered these effects, which were evident at this commercial scale, so we learned a lot”, says Bo Leckner.
Growing confidence prompted others to engage
In the subsequent unit, which was commissioned in 1991, the previous mistakes could be avoided. Bo Leckner had built up confidence in the technology among stakeholders outside Chalmers and managed to get the boiler manufacturers in the region, Vattenfall, the Gothenburg Energy and Building Board (Byggnadsstyrelsen, now known as Akademiska Hus), and the Swedish Energy Agency to engage in a joint venture. At that time, Akademiska Hus managed the operation of the boiler, as it does to this day. It operates the facility in accordance with the needs of the researchers, while ensuring the functioning of the heat source.
“It's very beneficial for us. Akademiska Hus takes care of all the problems, provides the personnel, and maintains the boiler, so that we can go there and do research”, comments Bo Leckner.
The predecessor of Valmet constructed both boilers.
“We had not been able to build such facilities on our own. Their knowledge on boiler making was required and they put together the boilers according to our wishes. In return, we could provide them with valuable knowledge about the fluidized bed technology”, says Bo Leckner.
Sharing the costs and outcomes
“It is a prerequisite for the success of the CPC that several parties have chosen to work together”, says Lars Strömberg, who started laboratory investigations of the fluidized beds. As a research manager at Vattenfall, he was involved in the construction of the second fluidized bed at the CPC, for which Vattenfall provided part of the financing.
“No single manufacturer or power company could fund a development on this scale. If one wants to develop and use the technology co-operation is essential, and if the costs are shared so also the results must be shared”, says Lars Strömberg.
The carbon dioxide-free power plant
After many successful years with using the fluidized bed technology, it was time for a completely new technology in the mid-1990s, as scientists called for the carbon dioxide-free power plant. The goal was to find a new combustion technology that would collect the carbon dioxide in the combustion process. As a research manager at Vattenfall, Lars Strömberg took the initiative to build the first experimental facility for oxyfuel at the CPC. The aim here is to obtain carbon dioxide of sufficient purity that it can be compressed into a liquid form, which can then be disposed of safely, thereby eliminating the carbon dioxide emissions from power plants that use coal, oil and other fuels.
“The technique proved to be excellent, and from the early 2000s, we have had several good studies and graduate students who have worked on various aspects of the technology”, says Lars Strömberg.
On standby for new technology
In 2006, Vattenfall built in Eastern Germany the pilot plant Schwartze Pumpe, which is based on oxyfuel technology and on the results obtained for carbon dioxide capture in the experimental facility of the power plant at Chalmers.
“Unfortunately, German politicians have decided to stop using coal, regardless of whether we can eliminate the problem of carbon emissions and despite the fact that it is both a technical and financial success”, says Lars Strömberg.
While the new-found reluctance to use coal has paralyzed research on oxyfuel systems, Lars Strömberg believes the politicians will rethink this policy when they realize that this technology is needed if we are to meet climate targets.
Non-traditional innovation
Lars Strömberg is confident regarding the future of the CPC, even if the project is questioned from time to time by people who do not realize its true value.
“This is not a traditional innovation process whereby scientists suddenly get a brainwave that can be commercialized. This is industrial process development in combination with scientific endeavor. This is something completely different that requires long-term cooperation, perseverance, and an awful lot of money. Just to build a plant takes several years”, says Lars Strömberg.
He believes that the key to success is the large-scale experimental research and the high scientific quality.
“This is what motivates these activities. That is clearly recognized by those who have insight into the business”, says Lars Strömberg.